Exploring the Advantages of Laser Welding vs Traditional Welding Methods
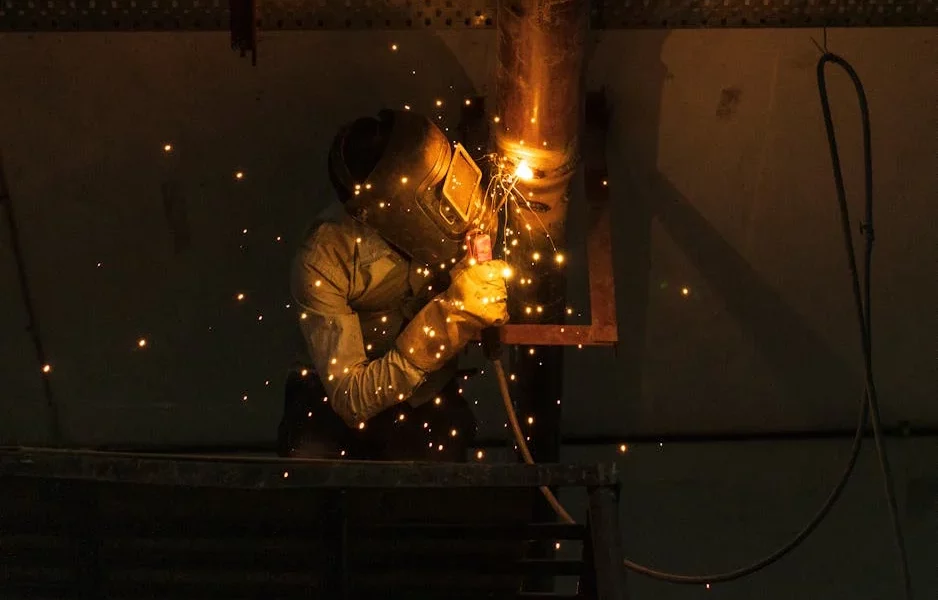
Laser welding, a highly sophisticated method that utilizes focused laser beams to melt and join materials, has gained significant traction in various industries. With advancements in technology, it offers several benefits compared to traditional welding methods, such as MIG and TIG welding. Understanding these advantages can help manufacturers and engineers make informed decisions about which welding technique to employ in their projects.
Precision and Accuracy
One of the standout benefits of laser welding is its exceptional precision and accuracy. The focused nature of the laser allows for highly controlled energy input. As a result, it minimizes the heat-affected zone (HAZ), leading to cleaner and stronger welds. Traditional methods can struggle with this precision, often resulting in larger HAZ and potential structural weaknesses. The team from eb industries says that this precision is particularly beneficial in the automotive and aerospace sectors, where even the slightest imperfections can lead to significant repercussions. Enhanced repeatability means that laser welding processes can maintain consistent quality, minimizing the risk of defects that might arise from manual operation.
Speed and Efficiency
Laser welding is renowned for its speed and efficiency, making it an attractive option for high-volume production environments. The ability to weld at a rapid pace reduces the overall time required for manufacturing processes, which, in turn, lowers labor costs. Traditional welding methods often require more time to ensure proper seam formation, which can hinder production speed. With advancements in high-power lasers, the welding process can operate at speeds that traditional methods simply cannot match. This increased efficiency is a game changer for manufacturers looking to boost their output while maintaining high-quality standards.
Cost-Effectiveness
While the initial investment in laser welding technology can be significant, the long-term benefits often outweigh these costs. The efficiency of laser welding translates to reduced cycle times and less energy consumption. Traditional welding methods may incur additional costs related to labor and materials due to potential waste from less precise welding. The durability of laser welds can reduce the likelihood of costly repairs and rework. Industries keen on maintaining profit margins are increasingly turning to laser welding as it provides a holistic approach to cost management.
Versatility in Applications
Another advantage of laser welding is its versatility. The method can be applied to a wide variety of materials, including metals, plastics, and ceramics, making it suitable for numerous industries, from medical devices to electronics. Traditional welding has limitations regarding material compatibility, often requiring specific techniques or filler materials to achieve acceptable results. The ability to weld dissimilar materials seamlessly is particularly valuable. For instance, combining metals with plastics has become more common in industries such as automotive and electronics. Laser welding facilitates these innovative designs, opening up new possibilities for product development.
Reduced Distortion and Heat Input
Laser welding’s low heat input significantly reduces the chances of thermal distortion. This is a crucial advantage for applications where maintaining dimensional stability is paramount. Traditional welding methods often produce considerable heat, which can lead to warping or changing the shape of components. With a more controlled process, laser welding ensures a higher degree of integrity in the materials being joined. This is essential for high-precision applications, where even minor distortions can compromise functionality.
Minimal Post-Weld Cleanup
Another standout feature of laser welding is the minimal requirement for post-weld cleanup. Traditional methods may leave excess slag or spatter, necessitating further cleaning or machining processes. Laser welding creates clean welds with little to no surface contamination, which not only saves time but also reduces finishing costs. This advantage is particularly beneficial in industries that demand high-quality finishes, such as in the manufacturing of consumer electronics or automotive components.
Automation and Integration with Modern Manufacturing
The rise of automation in manufacturing has also favored laser welding techniques. Laser systems can be easily integrated into automated production lines, enhancing overall workflow and efficiency. Traditional welding methods may require more manual intervention, which can lead to variability in results. Manufacturers may lower labor expenses and ensure consistent quality by integrating laser welding into automated processes. This integration supports the trend toward smart manufacturing, positioning businesses competitively in the market.
Environmental Considerations
As industries become more conscious of their environmental impact, laser welding presents a more sustainable option. The precise nature of the process ensures less waste material and reduced filler consumption compared to traditional methods. The lower energy requirements associated with laser welding contribute to a smaller carbon footprint. Organizations committed to sustainability find that laser welding aligns with their environmental initiatives, allowing them to meet regulatory requirements while maintaining productivity.
The shift toward laser welding over traditional methods is driven by a variety of factors, including precision, efficiency, cost-effectiveness, versatility, and environmental sustainability. As technology continues to advance, the advantages of laser welding are only expected to grow, making it a critical component in modern manufacturing strategies.